Two companies from the EPFL Innovation Park are transforming the best diagnostic method in Europe into a SaaS (software as a service) application for online use by property owners, who will be able to incorporate the requirements of cantonal climate plans into their building renovation choices or their portfolio property strategy, and put a figure on the cost.
History of innovation
The EPIQR (Energy Performance Indoor Quality and Retrofit) software was initially developed at EPFL in the 1990s by the Solar Energy Laboratory (LESO). A Swiss and European research success story, it has led to the creation of two start-ups in Switzerland and one in Germany, and has helped to create dozens of jobs in its 25 years of existence.
Hundreds of property owners and managers have found the tool they need to control the maintenance of their built assets and plan investment in the renovation of their buildings.
Thousands of buildings have been diagnosed using the software, and a large proportion have been renovated and energy-efficient.
EPIQR is a tool with a long history. In 1980, Professor Merminod from the University of Geneva set out to develop a method for calculating the cost of renovating a block of flats in a single working day (instead of a week). He then travelled around Europe to establish the state of the art and research on this subject. His journey led him to meet M. Maire, a French engineer from the Ponts et Chaussées who had developed the "Méthode d'Estimation Rapide" (MER) diagnostic method, as part of the implementation of the French social housing reform in 1979. Using a simple sheet of paper with boxes to tick and a calculator, this MER method made it possible to assess the cost of all the renovation work in record time.
Taking up this approach, the LESO-PB at EPFL developed the MERIP method in 1991 as part of a Federal Impulse Programme. The history of the MER paper form is the history of IT. It was transformed into an Excel sheet in MERIP, then into a Windows window in EPIQR, and in 2024 into a software as a service (SaaS), a window on the web opening onto an ecosystem of online software, with which the application can communicate, enabling different professions and service offers to work in synergy.
Energy transition 1.0
The third life of engineer Maire's method was brought to life by another EPFL professor, André Faist, founder of the Solar Energy and Building Physics Laboratory (LESO-PB) and director of this laboratory until the early 1990s. Prof. Faist's idea
Faist's aim was to offer designers a software tool that would enable them to combine the calculation of renovation costs with a simplified energy balance for the building. If homeowners accept a cost margin of +25% in the diagnostic phase," he said, "the possibility of easily establishing an energy balance would encourage them to include the cost of insulation in their budget (~5% of the total cost of the work) and would thus help to promote the energy-efficient renovation of buildings.
Once the EPIQR research project was completed in 1998, Prof. Faist encouraged Jean-Louis Genre and Flourentzos Flourentzou, who were working as assistants at LESO-PB at the time, to create an EPFL spin-off to bring the software to life and distribute it. The birth of Estia and EPIQR
Rénovation is the fruit of this process, and the two companies, based in the EPFL Innovation Park, have continued to work together on the development of the tool for over 25 years.
Inno Suisse takes over with EPIQR+
The fourth life of the method initially devised by engineer Maire is the result of a request from the real economy and, in particular, from the towns of Vevey, Neuchâtel, Lausanne, Grand-Saconnex and the State of Vaud, which wanted to work on the energy renovation of their school buildings.
To meet their needs, EPIQR Rénovation and Estia developed a project co-funded by Inno-Suisse (formerly CTI) to extend the scope of the method to all types of building. This project, carried out in collaboration with EPFL and SUPSI in Ticino, gave rise to EPIQR+.
The success of this new tool has enabled a number of major players to optimise control of their property maintenance and renovation investment budgets. EPIQR+ represents a turning point in the approach to renovation and acts as an accelerator of the energy transition by extending the database of costs taken into consideration.
European research takes renewed interest in EPIQR+
As part of another European research project (the PRELUDE project), EPIQR+ is currently being used to draw up a renovation roadmap.
The aim, for example, is to enable an expert carrying out a CECB+ energy analysis to complete his study by simultaneously analysing several renovation scenarios using EPIQR+. The tool is used in tandem with another method developed by European research, the Investimmo method, which can be used on a property scale to assess investment requirements, prioritise work using a multi-criteria method and plan work over time.
From high-energy standard renovation to low-carbon renovation
The very principle of refurbishing buildings can be likened to a large-scale recycling or reuse operation. The materials that make up the structure and envelope of an existing building represent a considerable 'non-emission' stock and, in the context of cantonal climate plans that aim to reduce CO2 emissions by 60% by 2030, optimising the renovation scenario becomes the keystone of the new ecological approach.
In the early stages of the energy transition, energy companies favoured major renovations to maximise energy savings. At the time, this led to a reduction in fossil fuel consumption (mainly gas and fuel oil) and the associated greenhouse gas emissions.
These days, buildings are increasingly heated by district heating networks, heat pumps or wood-fired boilers, so the CO2 emissions associated with heat consumption are much lower.
As a result, the energy, materials and resources used to carry out renovation work account for a growing proportion of the greenhouse gas emissions associated with the overall balance sheet of a renovation project. Energy efficiency must therefore go hand in hand with efficiency in the work carried out.
The new articles 117 and 118 of the Geneva LCI reflect this new awareness by targeting low-carbon construction and renovation. In a way, this law aims to avoid spending too much CO2 to reduce emissions.
Climate plans: a new chapter in the history of EPIQR+
The essence of engineer Maire's initial idea on the form has survived all the developments in IT because it had something ingenious about it: instead of statistically extrapolating the costs of works, he modelled them explicitly by element. This is how EPIQR+ has been providing credible, verifiable job costs with a high degree of accuracy (±15%) for 25 years. It is thanks to this that an owner has a structured, accurate and exhaustive diagnosis of the condition of his building or his property. And now, EPIQR+ CO2 can calculate the CO2 emissions associated with the works with the same speed and accuracy.
A climate plan is a property strategy which, in addition to controlling value and investment to preserve the quality of the built substance, aims to reduce CO2 emissions by 60% by 2030, with a view to achieving carbon neutrality by 2050.
The latest radical development in the method opens up new prospects, not only because it allows owners to control all the technical elements of a property strategy, but also because its new SaaS nature means it can work in partnership with an ecosystem of software or platforms, in particular energy monitoring, property valuation or energy optimisation platforms.
These innovations built into the new EPIQR+ confirm its positioning as a
as a benchmark tool in the renovation sector, and mark an important new chapter in its history.
We would like to thank the Office Cantonal de l'Energie genevois (OCEN), which co-financed the development of the method and provided free access to the CO2 database.
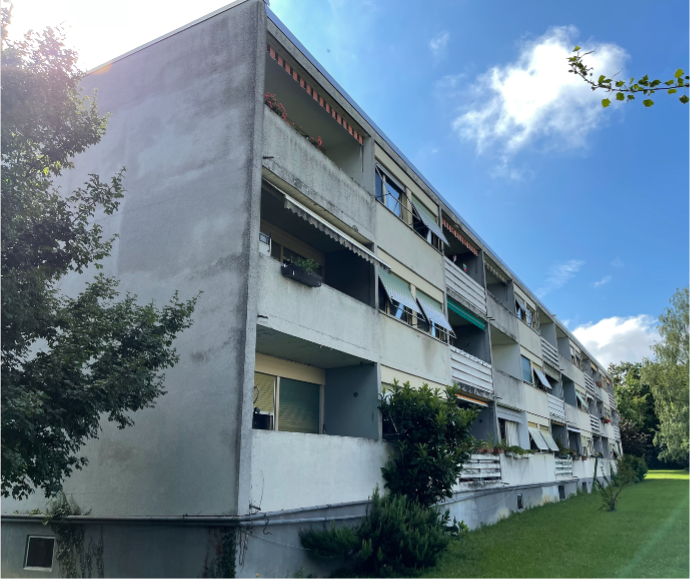
This 24-unit, oil-heated building in Geneva currently emits (before its renovation) 54 kgCO2 per year per m2 heated, or 104 tonnes of CO2. According to its ECCB, after an HPE renovation, connected to the CAD, it will emit 11.2 tonnes of CO2, whereas with an HPE renovation, it will emit 10 tonnes of CO2.
THPE it will reduce its emissions to 6.4 tonnes.
The new articles 117 and 118 of the Geneva LCI call for a low-carbon renovation concept that also accounts for the emissions generated by the work.
According to EPIQR+ CO2, the emissions from HPE renovation work are 9.5 tonnes of CO2, compared with 15 tonnes for THPE. The additional savings achieved by a THPE renovation are not enough to offset the emissions from the additional work (double flow, reinforced insulation, windows with reinforced insulation). According to EPIQR+CO2, these results do not
cannot be generalised.
On a larger building, with fewer envelopes per m2 heated, the THPE solution would be preferable, especially with low-carbon impact insulation.
FLOURENTZOS FLOURENTZOU
& JEAN-LOUIS GENRE